Warehouse Digital Twin is the Future of Warehouse Management for SMEs
- Robert Jurcec
- May 12
- 5 min read
Updated: Jun 10
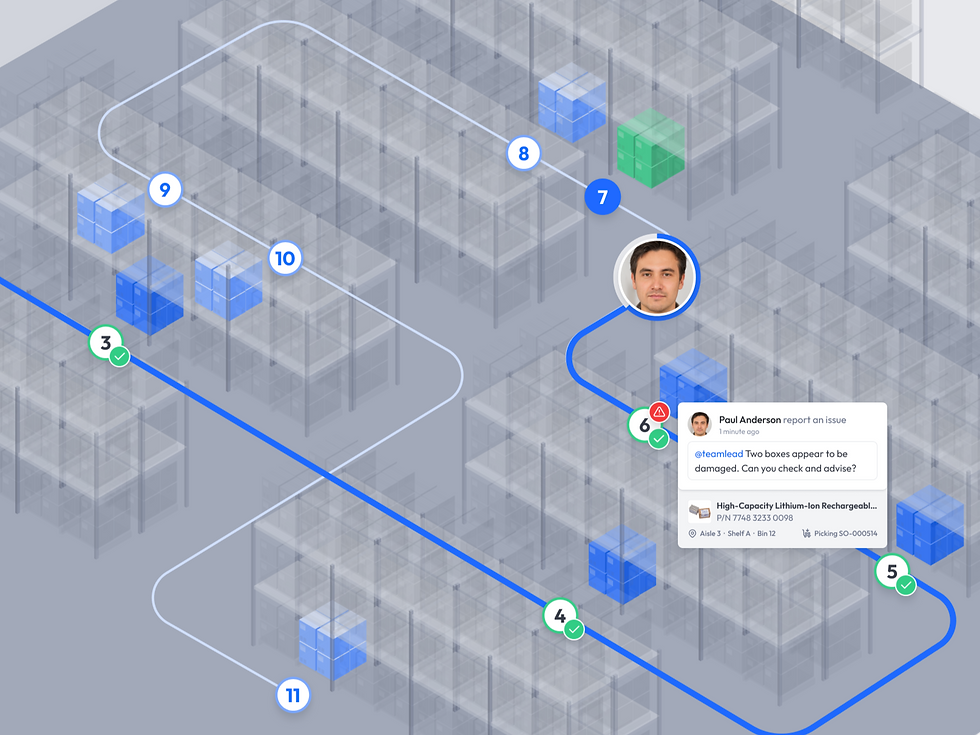
Warehouse management is undergoing a radical digital transformation. Traditional methods like spreadsheets, static maps, and even legacy WMS solutions are struggling to keep pace with today’s demands for real-time visibility, speed, and precision.
Enter warehouse digital twin technology in 3D, the new standard that is redefining how warehouses operate, optimise, and scale inventory management.
In this blog, we explore why 3D digital twins are the future of warehouse management, and how this game-changing technology increases operational efficiency by empowering operations to be faster, smarter, and more profitable.
What Is a 3D Digital Twin in Warehouse Management?
A 3D warehouse digital twin is a real-time, visual warehouse layout and virtual replica of your warehouse, including racks, pallets, forklifts, pickers, robots, and even live inventory movements. Unlike a simple floor plan or dashboard, a digital twin is fully dynamic, updating second by second as operations unfold through advanced simulation techniques.
Through a combination of IoT sensors, warehouse management systems (WMS), AI algorithms, and 3D visualisation, businesses gain a live, interactive modelling system they can monitor, analyse, and optimise remotely.
Primary Benefits of Warehouse Digital Twin Technology in 3D
1. Real-Time Visibility Like Never Before
Traditional WMS platforms provide data points but not the full operational context. With a warehouse 3D digital twin, warehouse managers can see the entire operation live: from real-time inventory locations and picker movements to the flow of forklifts or even AMRs (autonomous mobile robots). This comprehensive visibility allows managers to quickly identify bottlenecks, monitor safety risks, and optimise workflows as situations unfold. By bridging the gap between data and actionable insight, a digital twin transforms warehouse management into a proactive, agile process that drives efficiency and reduces costly errors.
Where inventory is located
Where pickers are working
Where bottlenecks are forming
How forklifts and AMRs (autonomous mobile robots) are moving
This level of real-time warehouse visibility, combined with warehouse safety technology, leads to faster decisions and fewer costly errors.
2. Faster Problem-Solving and Fewer Delays
When issues arise such as misplaced stock, blocked aisles, or equipment downtime traditional warehouses rely on manual inspections or radio calls to identify and resolve problems. This reactive approach often leads to delays and inefficiencies.
With a warehouse digital twin in 3D, warehousing problems are instantly visible on a central dashboard, enabling managers to respond in real time. Teams can quickly pinpoint the source of disruptions, coordinate solutions, and even anticipate potential issues before they escalate. This proactive capability streamlines operations, reduces downtime, and helps maintain a smooth workflow.
Rerouting pickers to avoid congested zones
Flagging missing pallets immediately
Assigning replenishment tasks dynamically
The result: faster shipments, more happ customers, and stronger SLA compliance
3. Slotting and Layout Optimisation Powered by AI
Using data from the 3D warehouse twin, AI algorithms continuously analyse stock movement, travel times, and picking patterns. They can recommend dynamic warehouse slotting and layout changes, seamlessly integrating with stock control software to optimise space and boost efficiency. These intelligent recommendations help reduce travel distances for pickers, minimise congestion, and ensure high-demand items are always within easy reach.
Over time, this data-driven approach leads to faster order fulfilment, lower operational costs, and a more agile warehouse that can quickly adapt to changing business needs.
Reduce walking distance for pickers
Optimise fast-moving SKUs placement
Improve cold storage efficiency
Over time, this AI-driven layout optimisation ensures the warehouse is not just running well, it is getting smarter every month.
4. Better Collaboration Across Teams and Sites
3D warehouse digital twins are cloud-based, meaning anyone from warehouse supervisors to regional directors can access the live model securely from anywhere. This universal accessibility breaks down communication barriers and ensures that everyone is working with the most up-to-date information. It becomes much easier to coordinate teams, monitor performance, and make informed decisions in real time.
As a result, collaboration improves across departments, and issues can be resolved faster, driving greater efficiency throughout the entire operation.
Coordinate multi-site operations for warehouse and inventory accuracy
Run remote inspections
Collaborate on warehouse redesign projects through effective warehouse collaboration
Train new staff virtually
With the growing trend toward distributed warehouses and micro-fulfillment centres, this remote management capability is critical.
5. Predictive Maintenance and Safety Monitoring
AA warehouse digital twin does not just track goods or manage inventory, it enhances warehouse problem-solving through smarter inventory management by continuously monitoring your warehouse health.
It provides real-time insights into equipment status, workflow efficiency, and safety compliance, allowing managers to quickly identify and address potential issues. By analysing trends and patterns, the digital twin helps anticipate maintenance needs, prevent bottlenecks, and optimise resource allocation. This holistic approach leads to a more resilient, agile, and productive warehouse environment.
Predict when forklifts need servicing
Spot safety risks like pedestrian-forklift conflicts
Identify equipment that’s being overworked
Proactive warehouse predictive maintenance reduces downtime and accidents, leading to lower insurance premiums and higher operational uptime.
Why 3D Digital Twins Are the Future, Not Just a Trend
Supply chains worldwide are being reshaped by four unstoppable forces that are driving businesses to rethink traditional approaches and embrace new solutions.
Companies that adapt quickly are gaining a competitive edge, while those that lag behind risk falling out of step with the market. As these trends accelerate, staying ahead requires agility, forward-thinking strategies, and a willingness to invest in transformative technologies.
E-commerce explosion (same-day delivery expectations)
Labour shortages (harder to find and keep warehouse staff)
Supply chain complexity (global disruptions, tighter margins)
Automation growth (robots, AMRs, AI scheduling)
3D digital twin technology directly addresses each of these challenges by making warehouses smarter, more agile, and highly responsive to change. By providing real-time visibility and actionable insights, digital twins empower managers to optimise operations, reduce waste, and quickly adapt to shifting demands. This technology also supports better decision-making by integrating data from multiple sources, enabling predictive maintenance, and enhancing overall efficiency.
As a result, warehouses become more resilient, competitive, and capable of meeting the evolving needs of the logistics industry.
Faster: dynamic task routing
Smarter: AI slotting and planning
Safer: real-time hazard detection
More scalable: remote multi-site control
Companies that adopt digital twin solutions early will outperform competitors who stick with outdated, reactive systems.
Real-World Example: 3DLogistiX Leading the Charge
Companies like 3DLogistiX are setting the benchmark with cutting-edge 3D visual warehouse mapping and live digital twin technology. By combining slotting optimisation, autonomous task assignment, and AI layout recommendations, they offer a truly future-ready platform that boosts warehouse performance by up to 30 – 40%.
In a world where every second, and every square metre, counts, this level of precision, integrated with solutions like Xero, MYOB, QuickBooks or Shopify for seamless financial management, is no longer optional.
Ready for a Smarter Warehouse?
3D warehouse digital twin technology is not just an innovation; it’s an essential evolution for inventory management. With real-time visibility, AI-driven optimisation, safer workflows, and smarter scaling, the warehouse digital twin model will soon become the new normal.
If you want your warehouse to move faster, run smarter, and stay competitive through 2025 and beyond, now’s the time to explore a 3D digital twin strategy.
Warehouses are evolving fast, do not get left behind. Book your 3DLogistiX demo now and step into the future of warehouse management